LED strip lighting is a popular lighting solution that offers versatility and adaptability for different lighting needs. In this article, we will discuss how to easily extend the LED strip light.
Switching off the LED strip light
The LED strip consists of small LED lights connected together to form a strip. The led strip is divided into modules with cut-off points at the end. The modules are electrically paralleled in the led strip, allowing the led strip to be cut and resumed.
So if you cut anywhere other than where you cut, the whole cut part of the series will be dark.
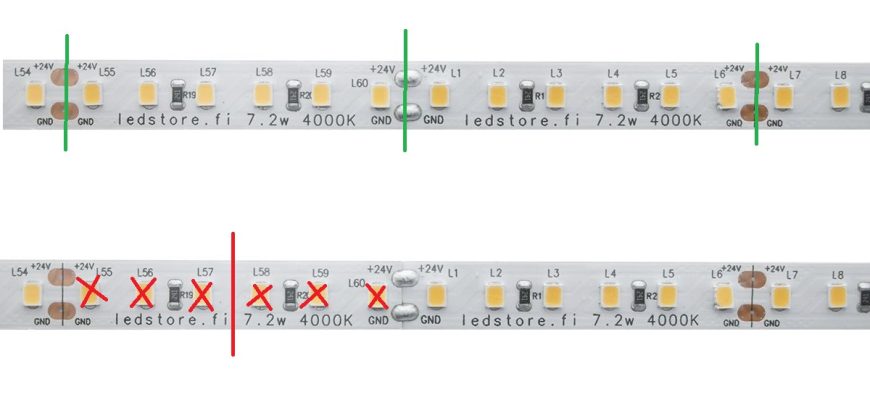
The low current 12V, 24V LED strip can therefore be cut off at intervals, depending on the LED strip light used… The cut-off points can be anything between 2.5 – 30 cm. The cut-off points are usually marked on the strip with small scissors pictures or a line. Cutting the LED strip – Cut the strip at the relevant point using sharp scissors.
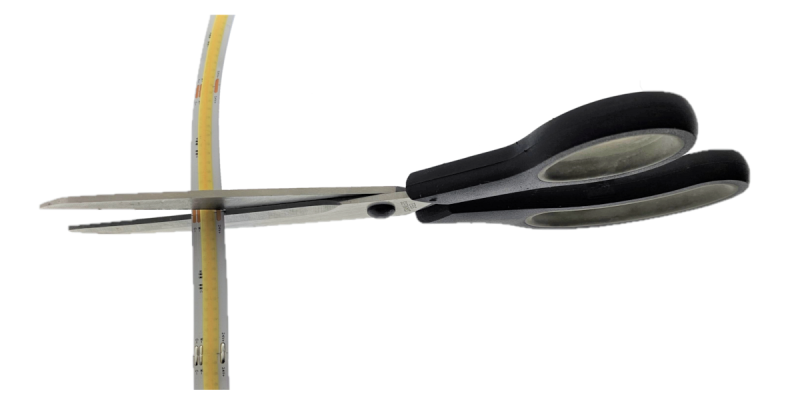
Led strip lighting soldering basics
Soldering a Led strip light is not impossibly difficult. You just need to understand the basics. Here are the instructions for soldering the Led strip.
Soldering iron
Almost anything will do as a soldering iron, and for years I used to use a cheap 8 euro soldering iron myself. If you do a lot of soldering, it’s certainly worth getting a better quality flask. But here are the main things to remember:
- Keep the flask as hot as possible – soldering is done quickly and not by heating for a long time
- Use the narrowest possible soldering tip – it makes it easier to get the heat only where you need it
- Keep the soldering tip clean – If there is burnt plastic, etc. on the soldering tip it will prevent heat production!
Soldering
There are many different types of watering can on the market. It helps a lot when soldering led strip lights if the tin is as narrow as possible. We use 0,5mm thick tin ourselves. Tin is sold in rolls and tubes.
There are many types of soldering tin available, but if you do a lot of soldering, leaded tin is best, e.g. 30/70 ratio. However, leaded tin is no longer sold to consumers, and you will need to have a Y-code to buy it. The ban is due to the toxicity of lead. You’ll do fine with other soldering stacks but the stickiness is just weaker, so it takes longer to warm up.
Whenever you do soldering work, remember to ventilate your workstation!
Led strip soldering
There are a few basic things to remember when it comes to the actual watering process, to make it as easy as possible.
- The tip of the soldering tin is always held on the surface where you want the tin to be.
- Hold the tip in place and bring the tin along the tip of the flask, right at the joint between the surface to be soldered and the tip.
Lead the soldering iron from the side to the joint between the piston tip and the copper - If the surface to be soldered is hot enough, the tin will run onto it. So don’t try to tin too hastily and make sure the soldering iron is hot enough. Test that the tin melts easily against the piston.
- Always carry out soldering work in good light and in such a way that you can see the surface well, and do not hit the LED circuit directly with the tip of the piston, as this can damage it.
- When connecting a wire to a strip or two ends of a strip, solder the tin to both surfaces first, i.e. the wire and the strip separately. Only then connect them together.
First solder the wire and the copper surface separately before connecting
LED strip light extension
For LED strips, there are connectors that allow the strip to be continued after it has been cut. Connectors sound easy, but from years of experience I can say that the only sustainable way to reconnect an LED strip light is soldering. Connectors get loose, dust and grease get in the way, and it’s hard to find connectors of the right size and quality. Another problem with off-the-shelf connectors is the versatility of LED strip lights, as there are many LED strip lights on the market, each of which can have solder points at different points, and the width of the LED strip light itself varies.
Why continue with the led strip lighting?
The LED strip can be extended and cut off for a variety of reasons. Most commonly, cutting and extending is done when you want to extend the tape or when there is a corner at the installation point. If you want to use the cut strip in several different places or if you want to adapt the length of the strip to different lighting needs, you will have to solder them with soldering irons.
On the other hand, learning the skill is useful and not impossibly difficult for basic LED strip lighting.

RGBW and RGBCCT may cause difficulties because of the 5-6 small solder points at the junction. How then to continue the light strip? Let’s now look at the tools and soldering in more detail.
Tools needed to extend the Led strip light
- Scissors – Sharp for cutting LED tape
- Soldering iron – Narrowest possible tip
- Soldering stacks – As thin as possible
- Silicone or shrink stick – for moisture protection
- Small hacksaw – For cutting aluminium profiles
These tools can therefore be used to extend the LED strip light. Silicone or shrinking plugs are required for wet room installations. In a dry room, you can just use electrical tape, or in many cases you can do without.
Steps to extend the Led strip light
- Measure the required length to the installation site
- I set the soldering iron to heat up, as hot as possible
- Cut led aluminium profiles
- Cut the led strips to size. Please note that the cut-off distance of the Led strip can be anything from 2,5 – 30cm, so please take this into account. In addition, 1-2 cm space is required for the wire connection at the end of the Led profile.
Remember to leave space for wires and solder in the profile - If you are using a wet room LED strip, cut away the protective layer from the solder points and clean off any adhesive stuck to the copper by lightly scrubbing if necessary.
- Solder tin to the soldering points on both ends of the LED strip.
First add the soldering iron to the strip - Place the ends of the extendable LED strip light opposite each other. Be careful that + and + are opposite, otherwise the led strip will be shorted from that point onwards and the light will not come on.
Remember to check that the ends of the tape are facing the right way - Heat between the ends, so that both solder stacks of the LED strip fuse together. Pull out the soldering iron, but DO NOT MOVE the led strips until the tin has hardened, otherwise the solder will fail.
Heat the soldering irons well - If the extension comes out, the extension should be protected with either a transparent shrink sleeve or silicone.
LED strip light extension at corners
The most common need for cutting comes at corners. The LED strip light does not bend 90° to the side. It should be cut and make a small splice with a soldering iron and cross the bend that way.
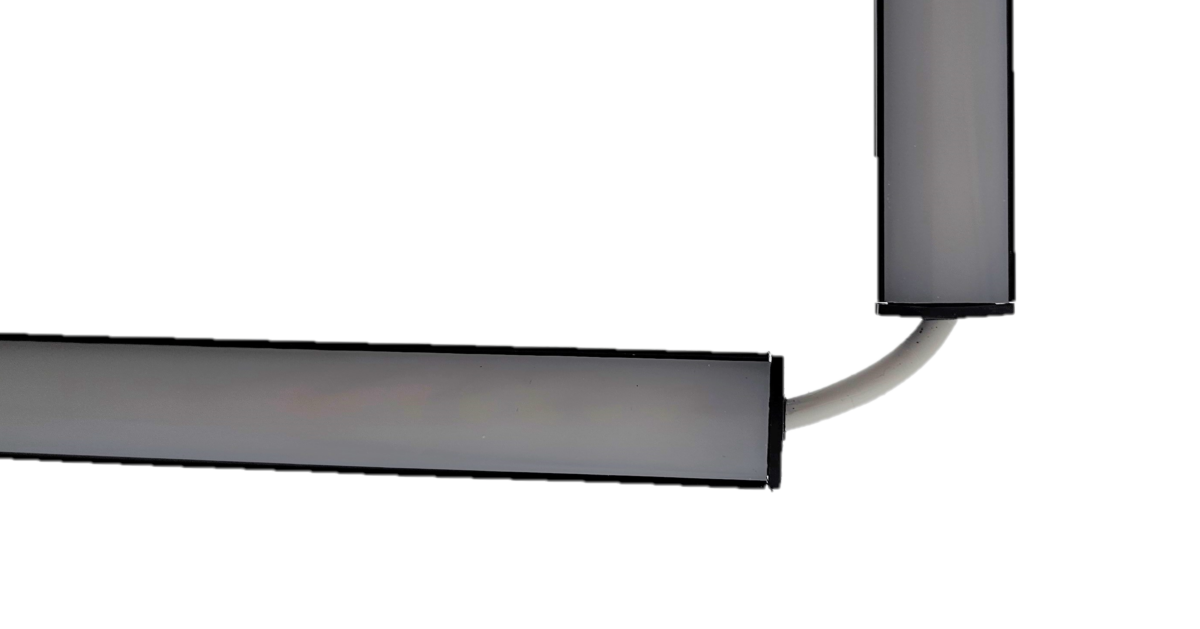
LED strip repair
If you have a faulty piece of LED strip light in the middle, it can be repaired using the same soldering instructions. We’ve gone through the process of replacing the part in more detail in the 12LED strip light cut-off guide.
Common mistakes and how to avoid them
One of the most common mistakes is cutting the led strip in the wrong place. It is important to cut the tape at the marked cut-off points to avoid damaging the tape and to allow it to be reattached.
Another common mistake is incorrect handling of the led strip after cutting. It is important to handle the ends of the cut tape correctly so that they are not damaged and the tape works properly. This applies to IP65 LED strips that are installed outside. An unprotected cutting head will collect moisture and damage the LED strip.
Summary
LED strip cutting is a simple process that requires only a few tools and basic knowledge of LED strip lighting. Switching allows the strip to be adapted to different lighting needs and spaces, making the LED strip a very versatile lighting solution.
I hope this article helped you understand how to disconnect and reconnect the LED strip light.
Led strip light installation guides
- 12Parallel connection of a Led strip light – We will discuss the principle of parallel connection and give an example.
- 12Led strip light cut-off – Led strip light cut-off and led strip light replacement
- 12Led strip light does not light – Why does led strip light not light, we go through the reasons
- 12Led strip light flashing – Why does a led strip light flash? There are many reasons and we will go through them all.
- 12Led strip light lifetime – What affects lifetime and why do other strips last longer?
- 12Led strip light mounting – How do I mount a led strip light indoors or outdoors? What needs to be taken into account?
- 12Connecting a led strip light to a transformer – How do I connect a led strip light to different types of transformers?
- 12RGB Led strip light connection – How do I connect an RGB led strip light to different control devices?
Led strip lighting specialist
LedStore has been an expert in LED lighting and lighting design since 2010. We have our own product design, so our products are technologically state-of-the-art. Products have quarantee for up to 7 years. We also carry out lighting maintenance.
We focus on temperature-controlled and high colour rendering lights, so they work brilliantly and last a long time. We do around 500 lighting designs for our clients’ sites in a year. Read more here or order a design. Did you know?
LedStore offers lighting design from 169 euros for the whole house!
Made to measure Led strip lights
We offer a service of custom-made led strips, i.e. custom-made led strips in aluminium profile. Also installed.
Remember that we are always ready to offer our help to you along the way, by email (myynti@ledstore.fi) and by phone (045 251 4510). Feel free to share photos of your own projects on social media at #ledstorefi IG and ledstore.fi FB. We love to see the cool things our LEDs do, and it helps to provide inspiration for those who are not sure about the power and awesomeness of LEDs.
Did you know that we already have over 3 500 pictures of our LED installations in our Gallery!